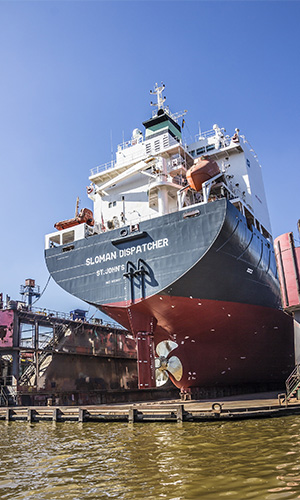
Ship’s hulls are protected against corrosion by coatings. However this is only a passive corrosion protection. In case of coating deficiencies corrosion is able to take off.
For this reason ships used galvanic anodes (zinc or aluminium) since over 100 years.
Nowadays ships use impressed current cathodic protection (ICCP) systems as a save corrosion prevention system together with appropriate coatings. These ICCP systems have a much longer lifetime because the anode consumption is more than a 1000 times lower than galvanic systems.
What does an ICCP system look like ? At under water level a series of inert anodes, mostly activated titanium, are distributed at both sides along the ship’s hull.
At the shaft and stern part, where different metals are used, which might be heavily touched by corrosion without cathodic protection, a big part of the anodes is located.
The ICCP system uses an external DC current, delivered by a transformer-rectifier, to feed the anodes. This creates a protection potential level of the steel wall.
In order to keep the protection level in a save zone reference electrodes, mostly zinc electrodes, are used to monitor the system.
Using a potential steered transformer-rectifier the cathodic protection system automatically reacts to changes in water quality and salt levels or the ship’s speed, which influence the electrical resistivity and thus the corrosion protection potential.
These ICCP systems may be controlled at distance by internet. Anotec’s Scotty RMU (remote monitoring unit) system provides the best solution because it is indicating the problem causes in case of a system failure. This information is send locally to the ship’s engineers but using internet may be communicated to the ship company’s help desk or service provider.